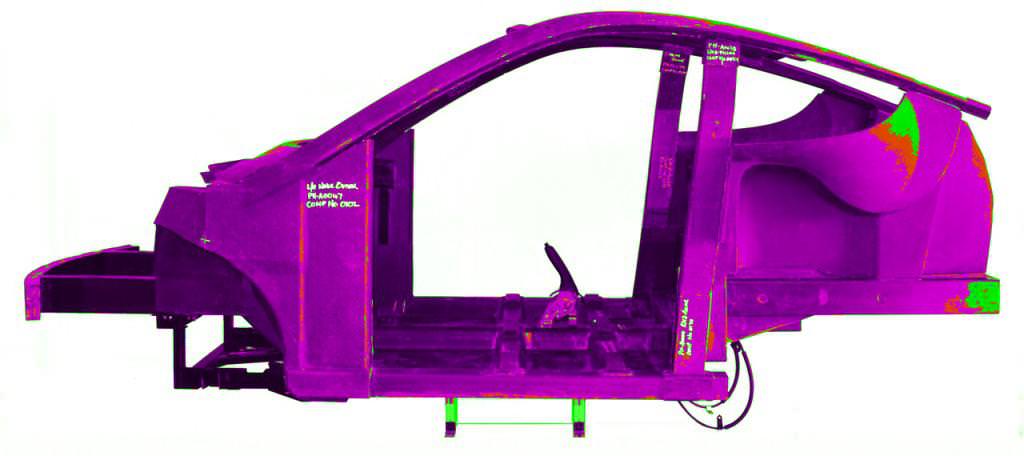
Ver traducción automática
Esta es una traducción automática. Para ver el texto original en inglés haga clic aquí
#Transportes: Automoción / Aeroespacio
{{{sourceTextContent.title}}}
¿No tan inverosímil?
{{{sourceTextContent.subTitle}}}
Las nuevas tecnologías se demandan para hacer cuerpos compuestos del vehículo asequibles en los pequeños volúmenes
{{{sourceTextContent.description}}}
La producción de chasis de la fibra de carbono es un costoso del del â del negocio apenas pide BMW. El vehículo-fabricante alemán y sus socios tienen entre ellos pasaron hacia arriba del ¬700m ($870m) del â en la producción en serie de sus modelos i3 e i8 que ofrezcan una gran cantidad de plástico fibra-reforzado carbono (CFRP). Por otra parte, estos costes no disminuyen mucho para los fabricantes bajos y del medio-volumen que miran para aprovecharse tiesura y del peso ligero del s del del materialâ de la alta. En 2010, por ejemplo, McLaren concedió un contrato valorado en el ¬150m del â al especialista austríaco CarboTech de los compuestos para producir aproximadamente 25.000 tinas del CFRP para sus supercars.
En base de estos ejemplos, uno pensaría que el uso del CFRP para la producción de componentes automotrices estructurales está restringido a los jugadores grandes y a los fabricantes sportscar de gama alta. Entre en Lejos-Reino Unido. Esta empresa pequeña en Nottingham, que emplea a alrededor 25 personas, ha desarrollado las tecnologías que demanda puede hacer el chasis del CFRP accesible y asequible para los fabricantes de automóviles del lugar con los volúmenes de la producción solamente de varios miles de unidades un año. Lejos-Reino Unido ha puesto en marcha una gama completamente de chasis obediente del CFRP de la desplome-prueba, llamó el chasis lejano de la plataforma (FPC), que se puede modificar para requisitos particulares por los fabricantes de automóviles a sus necesidades individuales de una variedad de maneras.
Según su fabricante, el FPC ligero y fuerte es simple montar y se puede incorporar en una variedad de líneas de montaje fácilmente. Optando por un spaceframe modular bastante que un diseño monocasco o de la tina, Lejos-Reino Unido puede fabricar cada FPC rápidamente usando útiles mínimos y métodos que moldean baratos. Además, el FPC puede recibir una variedad de diversos paneles del cuerpo para producir citycars, sportscars y las furgonetas, así como para acomodar una variedad de centrales eléctricas.
El FPC está disponible en tres variantes: sub-UNo, que tiene una distancia entre ejes de menos de 1,85 metros; A/B, que tiene una distancia entre ejes del del 2.0â 2,2 metros; y C/D, que tiene una distancia entre ejes del del 2.4â 2,6 metros. El chasis de A/B pesa apenas 65kg, encendedor algún 90kg que un chasis equivalente hecho del acero. El peso de bordillo máximo de un vehículo basado en este del del â del chasis incluyendo del del â de las baterías es 550kg, y su peso bruto máximo es 750kg.
El director de Lejos-Reino Unido, Lyndon Sanders, dice: el del del â esta estructura de la estupendo-luz tiene el potencial para entregar niveles récord de eficacia del combustible mientras que resuelve normas de seguridad rigurosas del desplome. Esto es un rato fantástico de estar en la industria del automóvil. Estamos en el cambio de signo de un del de wave.â
Orígenes académicos
Lejos-Reino Unido fue puesto en 2012 en la universidad del parque de la innovación de Nottingham y ahora actúa fuera de una instalación de 460 sq.m en el estado industrial de Wilford en Nottingham. La universidad tiene una reputación fuerte para la calidad de su investigación de los compuestos. Comentarios de las chorreadoras: del del â tenemos cierta lealtad; algunos de nuestros pensadores principales son de escuela de compuestos del s del de Nottinghamâ. No es una relación exclusiva, sin embargo; estamos trabajando con WMG [Warwick Manufacturing Group] en la universidad de Warwick y del NCC [los compuestos nacionales se centran] en la universidad del del de Bristol.â
Uno de objetivos principales del s del de Far-UKâ es hacerla más fácil para los fabricantes tales como fabricantes de automóviles y sus proveedores de la grada una para diseñar y para fabricar piezas compuestas. La compañía trabaja con sus clientes para desarrollar soluciones compuesto-basadas a los problemas que han probado difícil solucionar usando otros materiales. La central a la capacidad del s del de Far-UKâ de solucionar estos problemas es su cartera de las tecnologías del trenzado de la fibra de carbono.
El trenzado es un método para fabricar las materias textiles que data de los 1800s tempranos y se utiliza para producir cuerdas, cordones y las estructuras de refuerzo en mangueras de jardín. En un proceso que trenza convencional, un mandril se alimenta a través del centro de una máquina que trenza a una tarifa uniforme como hilados de la fibra de los portadores móviles en la máquina se deposita sobre la herramienta a una tarifa controlada. Los portadores funcionan en pares para producir un excesivo/bajo secuencia que trenza.
Como parte de su trabajo con el racimo de la innovación de los compuestos del s del de UKâ (CIC), Lejos-Reino Unido está desarrollando un proceso que implica trenzando el codenamed del del â del proceso 4 del del â que permite a las pequeñas y medianas empresas (SMEs) producir formas complicadas usando el CFRP en un precio asequible eliminando la necesidad de la equipar. Como demostración de su potencial, el proceso se ha utilizado para producir una silla de ruedas compuesta, que la compañía exhibió el año pasado en París en JEC Europa, un acontecimiento del buque insignia para la industria de los compuestos.
Construcción de la caja para Axontex
En agosto de 2013, Lejos-Reino Unido adquirió el axón automotriz de Wellingborough, Reino Unido. El axón fue establecido en 2006 para comercializar un proceso que trenzaba llamado Axontex. El directores técnicos y comerciales de s del de Far-UKâ, Kevin Lindsey y Chris Taylor, había estado trabajando en el axón antes de que pusieran a la compañía con las chorreadoras. Lindsey y Taylor habían iniciado muchos de los programas que estaban en curso en el axón, así que los pares sentían que su nueva compañía debe ayudar a su patrón anterior y a sus clientes en considerar estos proyectos a través a su conclusión.
“Pensamos que Axontex [trenzado compuesto] está listo para ir del del globalâ
Lyndon Sanders, Lejos-Reino Unido del del â
Las chorreadoras explican: del del â que conseguimos al punto donde estaba listo el propietario anterior del axón, que había arrastrado el negocio para arriba por sus tirantes nada, para retirarse. Con nosotros funcionando con la mayor parte de sus programas importantes, hicimos una oferta y asumimos el control a la compañía. Era un arreglo totalmente amistoso. Desde nuestro punto de vista, uno de los conductores dominantes para la adquisición era Axontex. Pensamos que Axontex está listo para ir del de global.â
Convertido inicialmente en la universidad de Cranfield en 1996, Axontex permite la producción de lazos y de aros de la fibra de carbono que se puedan combinar para fabricar las estructuras del haz del CFRP de una manera rentable. A diferencia del proceso 4, este tipo de trenzado requiere los útiles.
En abril de 2012, el axón automotriz fue presentado con un premio de la innovación en JEC para el desarrollo de un chasis del spaceframe para un del del â del coche de la ciudad del B-tamaño similar de tamaño a una Citroen C1 y llamó el del del â del axón 60 que pesó 50kg, producido usando Axontex. Los haces estructurales ligeros que fueron empleados para fabricar el spaceframe del axón 60 eran estructuras tridimensional tejidas, comprendiendo la trenza de la fibra de carbono sobre los objetos semitrabajados colocados a máquina múltiples hechos de la cerrado-célula, espuma del polietileno de baja densidad (LDPE).
Las fibras de carbono y el LDPE entonces fueron infundidos usando un proceso al vacío del moldeado de la resina-transferencia (VARTM) con una resina acrilato-basada uretano termoendurecible (Crestapol LV 1250 de Scott Bader de Wellingborough). Durante este proceso que moldea, la espuma de LPDE se amplía y se ajusta a la forma de la herramienta.
Los haces compuestos moldeados de la fibra de carbono de Axontex tienen una estructura interna única que ofrece las web del esquileo que, combinadas con las propiedades mecánicas de la resina, proporcionan alta tiesura y fuerza. Las muestras manufacturadas usando el sistema han exhibido una última resistencia a la tensión (UTS) del 1000MPa del 900â y de una temperatura de desviación de calor (HDT) encima de 130°C. El chasis pasó la prueba de carga del cinturón de seguridad según la regulación de ECE 14, resistiendo a daN hasta 1350 +/- 20 daN por el accesorio.
Cuenta del coste-beneficio
El uso de spaceframes trenzados presenta muchas ventajas sobre los métodos convencionales para la producción de chasis del CFRP. Los métodos largos de la endecha-para arriba de la mano usados por los gustos de Ferrari requieren el costoso del del â de los materiales con mucho del del â del despilfarro más laminadores altamente expertos y autoclaves costosas. El moldeo a presión de resina (RTM) empleado por BMW y McLaren requieren inversiones importantes en útiles y maquinaria. Por el contrario, Axontex genera poca basura, utiliza un material de la materia en trenza, y los útiles son baratos. Además, las máquinas de la infusión del vacío empleadas en el proceso son relativamente baratas.
Lejos-Reino Unido cree que los spaceframes de Axontex serían coste-competitivos con los marcos de aluminio que demuestran las mismas propiedades mecánicas cuando estaban producidos en plantas con salidas de las unidades del 35,0000 del aproximadamente 20,000â al año. Las plantas de coche convencionales usando unidades de acero presionadas de la producción considerablemente más que este del del â en alguna parte entre 100.000 y 150.000 unidades un pero ellas del del â del año emplean los útiles que pueden costar en la región del ¬400m del â un sistema. Un sistema de los útiles para la producción de bastidores de Axontex, por otra parte, costes menos que el ¬40m del â.
del del â estamos sacando órdenes de magnitud del coste de fabricación. No necesitamos producir esos volúmenes enormes para que nuestras plantas de Axontex hagan rentables, las chorreadoras del del del â explicamos. del del â que la discusión de fabricación distributiva entera comienza tan a golpear con el pie adentro. Si usted quiso hacer 100.000 unidades [usando Axontex], usted podría tener una planta en China que hacía 35.000 unidades, una en México que hacía 35.000 unidades y una en el Reino Unido que hacía 30.000 unidades; usted puede cubrir el del de globe.â
Lejos-Reino Unido ha utilizado las lecciones que aprendió con la adquisición de Axontex y la producción del axón 60 en el desarrollo del FPC. Cada variante del FPC se diseña alrededor de un solo sistema de útiles que Lejos-Reino Unido posea. La compañía suministrará el chasis bajo la forma de haces que sus clientes pueden pegar juntos ellos mismos, o como chasis completamente consolidado. El FPC se puede también suministrar como chasis rodante un sistema del parabrisas y de suspensión. Las chorreadoras continúan: el del del â si el cliente quisiera hacer la producción de volumen, en la región de 5000-10,000 unidades al año, nosotros diría que las valdría que tienen sus los propio anunció la fabricación, bastante que intentando acomodar sus necesidades con un estándar del de chassis.â
¿Qué clase de compañía estaría tan interesada en el FPC? En el Reino Unido, hay vario pequeño sportscar del del â de los fabricantes muchos cuyo está comenzado hacia fuera a vender el del del â de los equipo-coches que hagan aproximadamente 2,000-3,000 unidades al año. Estas compañías sobreviven en el aspecto y el funcionamiento de sus vehículos, y podrían bien estar interesadas en las ventajas potenciales proporcionadas por FPC. Fuera del Reino Unido, hay muchos fabricantes a escala reducida produciendo los vehículos que son más utilitarios en naturaleza, tal como citycars y vehículos de entrega híbridos.
del del â también estamos teniendo conversaciones con varias compañías más emprendedores que sean nuevos participantes a este mercado, particularmente en la producción de vehículos eléctricos; las compañías que no están en ese espacio en el momento, pero creen que los vehículos eléctricos son la manera adelante, del del â revelan las chorreadoras. el del del â estas compañías se podría suspender por la cantidad de ingeniería necesaria para entrar en ese mercado, así que alguien que podría ofrecer esa ingeniería en un formato rodante del chasis es un amigo potencial. Estas conversaciones están sucediendo tanto en el interior como en el exterior del de Europe.â
¿Una segunda vida?
Los directorios de la fin-de-vida de la unión europea estipulan que los 80% de los materiales usados en un nuevo coche tienen que ser reciclables. ¿Cuáles son tan las opciones para el FPC? Hay una manera relativamente directa de reciclar el CFRP: puede ser molido para arriba y ser utilizado como llenador en hormigón. Métodos más sofisticados que esto, tal como pirolisis (en las cuales la matriz de la resina esencialmente se quema apagado, rindiendo fibras de carbono) también se están madurando.
Sin embargo, Lejos-Reino Unido tiene una solución más interesante a este problema. Cree que su FPC es bastante durable sobrevivir al resto del coche. Como tal, un fabricante de automóviles podría producir un vehículo se vuelve y para arriba-se completa un ciclo que en el extremo de su del del lifeâ del del del â primer. Por ejemplo, el exterior del del â de los paneles de piel que se pudo hacer del fibra-reforzado de cristal del del â del plástico (GFRP) contribuir al aspecto del vehículo pero no a sus propiedades estructurales. Estos elementos se podían pelar y substituir para restaurar el aspecto del coche. Además, el diseño de FPC puede acomodar una variedad de diversas centrales eléctricas, así que éstos podrían también ser alterados.
Las chorreadoras explican: el del del â El FPC pudo salir la fábrica con una central eléctrica híbrida de la gasolina en él, puede ser que haga 100.000 millas en diez años y entonces puede ser que se vuelva. El fabricante pudo pelar los todos los paneles exteriores, saca el powertrain de él, poner una pila de combustible del hidrógeno en ella, re-piel él y ponerla detrás hacia fuera sobre el camino otra vez. El marco será fino. Ésta es una discusión que tiene todavía ser probada con la UE en términos de sus directorios de la fin-de-vida, pero sostendríamos que la reutilización es mejor que del de recycling.â
Lejos-Reino Unido ahora está apuntando el otro extremo del mercado automotriz. Está trabajando con Tata Motors European Technical Centre (TMETC) en un proyecto de £3m para desarrollar un proceso para la fabricación en grandes cantidades de componentes estructurales baratos, ligeros. Según el encargado de programa técnico del s del del companyâ, Sophie Cozien-Cazuc, el proyecto de HiLiTe ofrecerá las soluciones técnicas que permitirán a los fabricantes de automóviles considerar seriamente los materiales plásticos fibra-reforzados para sus plataformas futuras.

{{medias[774].description}}
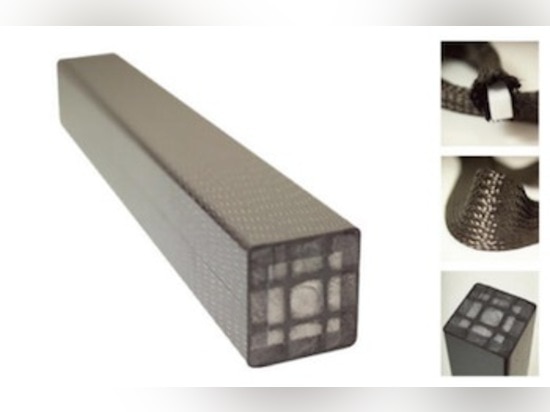
{{medias[775].description}}
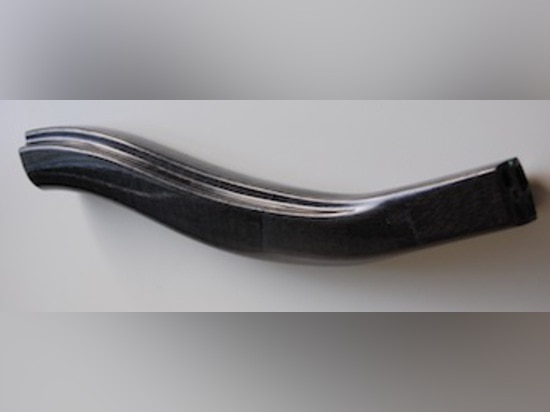
{{medias[776].description}}